Hay Pole Barns in Aberdeen: A Closer Look at How Pole Barns Are Built
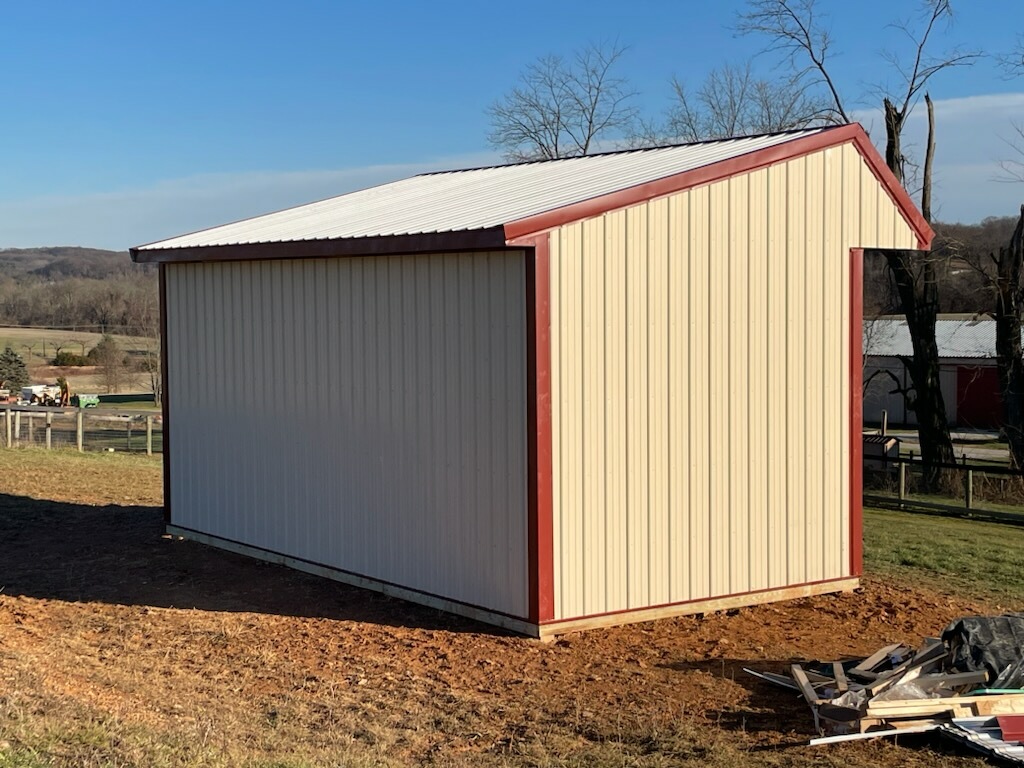
Hay Pole Barns in Aberdeen: A Closer Look at How Pole Barns Are Built — If you travel over Aberdeen or the nearby countryside, you probably will notice more than a few tall pole barns dotting wide fields. Affordability, durability, and straightforward design are well-known qualities of these adaptable buildings. Still, one of the most often asked questions we get at Fetterville Sales is, “How are pole barns built?”
This is particularly pertinent in relation to hay pole barns in Aberdeen, where storage requirements, land topography, and year-round temperature conditions all factor. Building a pole barn goes beyond merely laying four walls and a roof. This methodical procedure combines clever engineering with sensible planning to produce a construction capable of decades of use.
We will review the main phases of pole barn building and discuss why so many Aberdeen landowners select this approach for agricultural use and hay storage.
Step 1: Site Selection and Preparation
Every great edifice begins on the ground it stands upon. Starting each project involving hay pole barns in Aberdeen, we evaluate the site considering soil characteristics, grading requirements, water runoff, and access points. The intention is to select a level, well-drained site conveniently accessible for tractors, trucks, or machinery.
Once the location is chosen, any plants, trash, or impediments are removed. The surface is then leveled and occasionally compacted to offer a solid, even basis. Site preparation for hay barns might also involve laying a gravel pad or foundation layer to reduce muck and moisture under the construction.
Step 2: Layout and Footings
Once the site is ready, we start drawing out the precise footprint of the pole barn. This covers determining and designating the sites of the support posts, often known as “poles.” The structural integrity of the structure depends on the design, size, and intended use of the barn, thereby determining the distance between these posts.
Next, depending on local laws, frost lines, and the size of the construction, post holes are drilled—usually 3 to 6 feet deep. Concrete footings are often poured into these holes to sustain the weight of the posts and provide long-term stability. In Aberdeen, where winter freeze-thaw cycles can cause ground movement if not adequately considered, this is especially crucial.
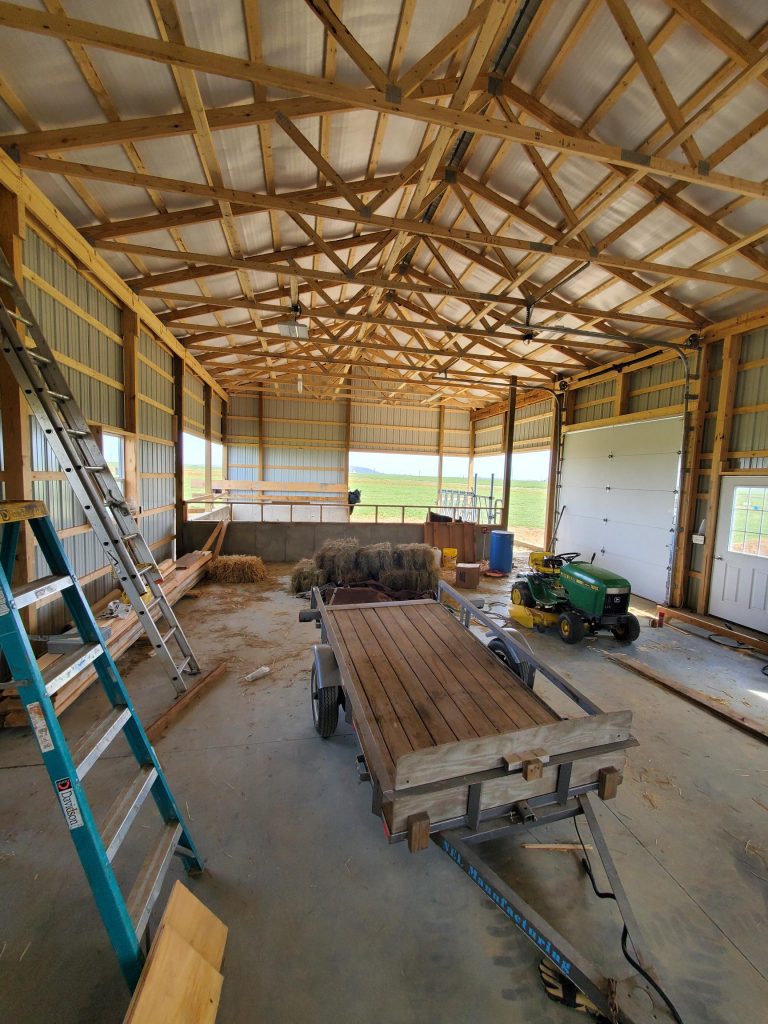
Step 3: Setting the Posts
Once the footings are in place, the vertical support posts are installed. Usually, pressure-treated hardwood posts were selected for their resistance to dampness, insects, and rot and for their strength. To make sure the barn is square and level, each post is positioned precisely in its assigned hole and aligned with string lines or laser levels.
Depending on site circumstances and the demands of the construction, the posts are then fixed by tamped gravel or concrete backfilling the hole. These posts will support the siding, roof trusses, and any internal framework, therefore forming the skeleton of the whole barn.
Step 4: Installing Girts and Trusses
Now it’s time to link the posts horizontally using boards known as “girts.” These form the mounting points for the outer walls of the barn and give lateral stability. Trusses or rafters set at the top of the posts support the roof construction.
Usually pre-engineered, the trusses—dependent on the project—are either brought to the site or fabricated there. Particularly in a climate like Aberdeen’s, where snow and wind might be problems, hay pole barns in Aberdeen must have the proper roof pitch and truss strength to carry a large amount of weight.
Step 5: Framing the Roof and Walls
Purlins—horizontal roof supports—are placed once the trusses are in place. These provide the roof panels a solid basis and help to support the barn generally. Once the roof structure is finished, wall framing takes center stage.
Particularly helpful for hay storage, some barns have open sides for airflow; others are enclosed with wood, metal, or composite panels. Depending on the use of the structure, this stage also involves window and door opening framing.
Step 6: Adding Siding and Roofing
Now the barn should start to take shape visibly. Because of its minimal maintenance, weather durability, and lifetime, steel siding and roofing are the most often used choices. Over the framework, these panels are set and fastened with screws used to manage water resistance and wind uplift.
Because color choices and finishes vary greatly, Aberdeen hay barns have clients that generally select tones that complement nearby structures or fit the landscape. At this point, gutters, ridge vents, and roof overhangs—especially if the barn will be utilized year-round for cattle—are also built.
Step 7: Interior Features and Finishing Touches
The last stage, depending on the client’s demands, consists of any internal build-out, including lofts, storage spaces, or walls. Aberdeen hay barns could need strengthened floors, ventilation systems, or racks for better stacking and airflow.
When needed, at Fetterville Pole Buildings we can provide alternatives that include insulation, lighting, electrical systems, and concrete floors. Many hay barns are still open and basic, while others are multi-use structures that go beyond simple storage needs.
Why the Process Matters
A hay pole barn in Aberdeen, built correctly, can survive forty to sixty years or more. Working with a builder who appreciates the detailed approach and treats every aspect carefully is therefore absolutely vital. In Aberdeen, where property management and farming are major businesses, you need a long-term rather than a temporary repair structure.
Over the decades, Fetterville Sales has honed its technique to provide every barn we create with efficiency, longevity, and workmanship. From big enclosed structures to little hay huts, our crew works on every project with respect for your property and objectives and great attention to detail.
Final Thoughts: How Are Pole Barns Built?
Pole barns are, all things considered, strong, straightforward, and flexible constructions. Every action, from laying ground pillars to fastening the last roof panel, helps to produce a structure that will resist time and weather.
Fetterville Sales is here to help you navigate the process should you be looking at hay pole barns in Aberdeen. Whether your demands call for simple storage or a fully equipped building, we will assist you in creating a barn that not only satisfies but also exceeds your requirements.
Fetterville offers top-notch farm buildings, custom pole barns in Aberdeen, horse barns, and more.
With more than forty years of industry knowledge, trust Fetterville Pole Buildings for affordable pricing, competent service, and unmatched quality in post-frame construction. Let us add you to our extensive list of pleased clients.
Fetterville Sales has been your reliable friend since 1980 when it comes to pole barn garages and Amish pole buildings in Aberdeen. Our dedication to individualized service starts with an initial face-to-face meeting so that we can fully grasp your demands. For pole construction solutions, our Amish pole barn builders in Aberdeen will provide the knowledge and commitment to quality that you’ve been looking for.
Our horse barn builders in Aberdeen will go in-depth, covering everything from design choices to financial constraints. Together, we will create a plan to make sure that your new building offers a personalized solution that fits your vision and satisfies your expectations.
Main Office: East Earl, PA 1-800-331-1875
Western Office: Bridgeville, PA at 1-800-275-8245